Structure of sintered brick drying kiln
Industry news | Refractory Wiki | Refractory news | Enterprise news | Structure of sintered brick drying kiln
The tunnel kiln to dry bricks is called a drying kiln, which completes the various processes of sintered bricks in conjunction with the roasting kiln. As one of the links in the production process, it plays an important role.
01
Specification
The length of the drying kiln is between 60 and 136m. In the few years that the tunnel kiln has just been popularized in my country, most of the drying kilns built are shorter, and the length is between 60 and 90m. The layout of the three drying sections of medium temperature and high temperature is too compact, which is one of the reasons for non-drying, cracks, and collapse, which restricts the production capacity and quality of the kiln.
The length of the drying kilns built in recent years has been extended, laying the foundation for a good drying effect. The length is between 102~136m, and the longer drying kiln is supplemented by reasonable moisture removal, heating facilities and standardized operation, so the drying effect is still satisfactory.
The internal width and height of the drying kiln are equal to that of the roasting kiln, that is, the gap between the sides and the top of the billet stack should be between 8 and 12 cm, which is convenient for the operation of the roasting kiln. There is a view that the internal height of the drying kiln should be 36~58cm higher than the upper brick, and the excess headspace is beneficial to the smooth drainage of moisture. In fact, this is wrong.
In the drying kiln I commissioned, the drying effect of this type of structure is poor. The reason is that the space at the top causes the stratification of temperature and air flow, the cold and heat exchange law in the middle and lower parts of the billet stack is low, and the huge space at the top needs sufficient temperature to fill. That is to say, the temperature in the entire drying kiln is very easy to lack, and the drying effect is often unsatisfactory.
02
Tide
The function of the moisture exhaust system of the drying kiln is to extract the moisture generated during the drying process of the bricks from each moisture exhaust port in the state of moisture and flue gas, and then discharge to the outside through the moisture exhaust flue, fan for dust removal and desulfurization.
There are two types of tidal discharge methods: centralized and scattered. Centralized tidal discharge refers to the construction of the tidal flue from the 2 parking spaces at the billet inlet end to the 10 to 12 parking spaces at the rear. It is improper that some centralized moisture exhaust ducts have only 6 to 8 parking spaces in length, causing the temperature and the flow of smoke to be forward, and the condensation is serious in cold weather, resulting in different degrees of collapse.
Dispersed moisture exhaust means that the exhaust flue starts from the 2 parking spaces at the billet inlet end to the 18-22 parking spaces behind. If the dispersion and drainage are short, the subsequent temperature and moisture return will be serious, which will become the cause of collapse and cracks.
The moisture exhaust fans are installed in 1~3 parking spaces on the top of the drying kiln, and some are also placed under the drying kiln. Some drying kilns with separation of smoke and heat are composed of 3~5 axial fans, which are installed in sections in the drying kiln. the top of. However, from the perspective of easy management and operation, the use of a centrifugal exhaust fan is recommended.
The moisture exhaust flue is built on both sides or top of the drying kiln, the moisture exhaust of the integrated kiln is in the lower part of both sides, and the moisture exhaust flue of the split kiln drying kiln is generally built on the top. The internal height of the tidal flue at the top is between 1.6~2.5m,
The width is equal to the section size of the kiln. The moisture exhaust flue with a large internal space is easy to adjust during use. There are multiple moisture exhaust openings in the moisture exhaust flue. The interval size is 1.8~2.5m. The width of the exhaust opening is 22. ㎝ about, the length depends on the situation. Each drain outlet is equipped with a gate valve to adjust the size.
03
Heating
Heating is used as a heating system for drying bricks. Due to the different drying modes, heating can be divided into two types: the heating starts from the first and second parking spaces at the charging end, or from the middle and rear of the drying kiln.
The heat-supply fan extracts the smoke heat and waste heat from the roasting kiln and blows it into the heating flue. The hot air pressure is conveyed to the drying kiln through the dispersed heating vents.
The centrifugal fan is better for the heating fan, and the performance is better than that of the axial fan in terms of blowing force or ease of maintenance.
There are two modes for the operation of the hot air blower, one is to supply heat to the drying kiln and the flue gas of the roasting kiln; the other is to extract only the waste heat from the insulation belt of the roasting kiln and transport it to the drying kiln, that is, the smoke and heat separation type.
The heating flue is made of two types of materials: brickwork and iron pipes, each of which has its own length and performance. The heating flue pays attention to good heat preservation, tight sealing and smooth ventilation.
There should be insulation facilities outside the heating flue to avoid the loss of heating temperature. The tight sealing prevents the smoke from spreading to the top of the kiln and polluting the environment.
The heating flue should minimize the bends and sharp turns, and the internal size should be changed according to the section of the kiln. The larger the section, the larger the internal size. Inside and outside of the heating flue, there are lower side, upper side and top heating ports. The lower side heating ports account for most parking spaces, the upper side and roof heating occupy 5 to 8 parking spaces, and the upper side and top heating ports are distributed in the drying kiln. The high temperature area in the back section.
The width and height of the side heating ports are generally 6.5×36 cm, with an interval of about 110 cm. The size of the top heating port is a bit larger. Regardless of the side heating port or the top heating port, it is best to aim at the fire channel gap of the billet stack, and guide the hot air pressure to blow into the billet stack, creating conditions for improving the heat-cooling exchange law.
04
other
A kiln door is installed at both ends of the billet inlet and outlet of the drying kiln, and most kilns have a kiln door only at the billet inlet end. There are two kiln doors installed. When loading wet bricks into the kiln, first lift the first kiln door to load the billet car, close the first kiln door, lift the second kiln door, and continue to push the billet car in.
The advantage of the two kiln doors is to reduce the internal absorption of cold air from the outside, to ensure the normal operation of internal pressure and temperature, and to stabilize the oxygen content in the discharge.
The temperature control system is more and more used in the drying of bricks. The thermocouple is connected to the computer temperature display, and the temperature data of each drying section can be known at any time. Based on this, timely adjustment is brought to the standard and efficient drying operation. convenient.
The thermocouple is installed on the top and lower side of the drying kiln, and the specific positions are: near the heating fan, the exhaust flue, 3 parking spaces, 8 parking spaces, 15 parking spaces, 21 parking spaces, and 26 parking spaces.
Several observation windows are set on the top of the drying kiln and on the wall of the kiln to keep abreast of the internal temperature and humidity conditions, so as to be targeted for proper operation.
The position of the observation window is: 3, 5, 7, 9, 11, 12, 15 parking spaces, and the corresponding position of the observation port is preferably the blank stack fire channel, which provides convenience for expanding the observation area.
Environmental emission requirements are becoming stricter and stricter, and the brick and tile industry is no exception. The drying kiln should be considered at the beginning of the construction and design, such as the desulfurization and dust removal devices are large in size and heavy, and it is more appropriate to install under the drying kiln.
The regulation of oxygen content starts from blocking the air leakage point and guiding the digestion. The kiln wall, kiln roof, kiln door and moisture exhaust flue should be airtight and tight, and the observation ports that are not used temporarily should be pasted. In some drying kilns, a moisture exhaust fan is installed between 2-6 parking spaces at the billet inlet end, and the exhausted flue gas is transported to the kiln end of the roasting kiln to be used as combustion air for secondary combustion, which has a significant oxygen reduction effect.
The tidal exhaust fan only extracts the gas from a few parking spaces close to the kiln door, intercepting the excessive oxygen caused by the leakage of the kiln door, and only extracts the gas at the initial stage of drying, which contains relatively small flue gas and moisture, and is transported to The roasting kiln has little effect on roasting as combustion air. After the 6th parking lot, another damp exhaust fan is responsible for the exhaust, and the extracted flue gas is transported to the outside for desulfurization and dust removal.
The tunnel kiln to dry bricks is called a drying kiln, which completes the various processes of sintered bricks in conjunction with the roasting kiln. As one of the links in the production process, it plays an important role.
01
Specification
The length of the drying kiln is between 60 and 136m. In the few years that the tunnel kiln has just been popularized in my country, most of the drying kilns built are shorter, and the length is between 60 and 90m. The layout of the three drying sections of medium temperature and high temperature is too compact, which is one of the reasons for non-drying, cracks, and collapse, which restricts the production capacity and quality of the kiln.
The length of the drying kilns built in recent years has been extended, laying the foundation for a good drying effect. The length is between 102~136m, and the longer drying kiln is supplemented by reasonable moisture removal, heating facilities and standardized operation, so the drying effect is still satisfactory.
The internal width and height of the drying kiln are equal to that of the roasting kiln, that is, the gap between the sides and the top of the billet stack should be between 8 and 12 cm, which is convenient for the operation of the roasting kiln. There is a view that the internal height of the drying kiln should be 36~58cm higher than the upper brick, and the excess headspace is beneficial to the smooth drainage of moisture. In fact, this is wrong.
In the drying kiln I commissioned, the drying effect of this type of structure is poor. The reason is that the space at the top causes the stratification of temperature and air flow, the cold and heat exchange law in the middle and lower parts of the billet stack is low, and the huge space at the top needs sufficient temperature to fill. That is to say, the temperature in the entire drying kiln is very easy to lack, and the drying effect is often unsatisfactory.
02
Tide
The function of the moisture exhaust system of the drying kiln is to extract the moisture generated during the drying process of the bricks from each moisture exhaust port in the state of moisture and flue gas, and then discharge to the outside through the moisture exhaust flue, fan for dust removal and desulfurization.
There are two types of tidal discharge methods: centralized and scattered. Centralized tidal discharge refers to the construction of the tidal flue from the 2 parking spaces at the billet inlet end to the 10 to 12 parking spaces at the rear. It is improper that some centralized moisture exhaust ducts have only 6 to 8 parking spaces in length, causing the temperature and the flow of smoke to be forward, and the condensation is serious in cold weather, resulting in different degrees of collapse.
Dispersed moisture exhaust means that the exhaust flue starts from the 2 parking spaces at the billet inlet end to the 18-22 parking spaces behind. If the dispersion and drainage are short, the subsequent temperature and moisture return will be serious, which will become the cause of collapse and cracks.
The moisture exhaust fans are installed in 1~3 parking spaces on the top of the drying kiln, and some are also placed under the drying kiln. Some drying kilns with separation of smoke and heat are composed of 3~5 axial fans, which are installed in sections in the drying kiln. the top of. However, from the perspective of easy management and operation, the use of a centrifugal exhaust fan is recommended.
The moisture exhaust flue is built on both sides or top of the drying kiln, the moisture exhaust of the integrated kiln is in the lower part of both sides, and the moisture exhaust flue of the split kiln drying kiln is generally built on the top. The internal height of the tidal flue at the top is between 1.6~2.5m,
The width is equal to the section size of the kiln. The moisture exhaust flue with a large internal space is easy to adjust during use. There are multiple moisture exhaust openings in the moisture exhaust flue. The interval size is 1.8~2.5m. The width of the exhaust opening is 22. ㎝ about, the length depends on the situation. Each drain outlet is equipped with a gate valve to adjust the size.
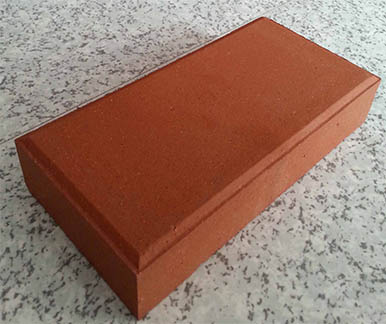
Heating
Heating is used as a heating system for drying bricks. Due to the different drying modes, heating can be divided into two types: the heating starts from the first and second parking spaces at the charging end, or from the middle and rear of the drying kiln.
The heat-supply fan extracts the smoke heat and waste heat from the roasting kiln and blows it into the heating flue. The hot air pressure is conveyed to the drying kiln through the dispersed heating vents.
The centrifugal fan is better for the heating fan, and the performance is better than that of the axial fan in terms of blowing force or ease of maintenance.
There are two modes for the operation of the hot air blower, one is to supply heat to the drying kiln and the flue gas of the roasting kiln; the other is to extract only the waste heat from the insulation belt of the roasting kiln and transport it to the drying kiln, that is, the smoke and heat separation type.
The heating flue is made of two types of materials: brickwork and iron pipes, each of which has its own length and performance. The heating flue pays attention to good heat preservation, tight sealing and smooth ventilation.
There should be insulation facilities outside the heating flue to avoid the loss of heating temperature. The tight sealing prevents the smoke from spreading to the top of the kiln and polluting the environment.
The heating flue should minimize the bends and sharp turns, and the internal size should be changed according to the section of the kiln. The larger the section, the larger the internal size. Inside and outside of the heating flue, there are lower side, upper side and top heating ports. The lower side heating ports account for most parking spaces, the upper side and roof heating occupy 5 to 8 parking spaces, and the upper side and top heating ports are distributed in the drying kiln. The high temperature area in the back section.
The width and height of the side heating ports are generally 6.5×36 cm, with an interval of about 110 cm. The size of the top heating port is a bit larger. Regardless of the side heating port or the top heating port, it is best to aim at the fire channel gap of the billet stack, and guide the hot air pressure to blow into the billet stack, creating conditions for improving the heat-cooling exchange law.
04
other
A kiln door is installed at both ends of the billet inlet and outlet of the drying kiln, and most kilns have a kiln door only at the billet inlet end. There are two kiln doors installed. When loading wet bricks into the kiln, first lift the first kiln door to load the billet car, close the first kiln door, lift the second kiln door, and continue to push the billet car in.
The advantage of the two kiln doors is to reduce the internal absorption of cold air from the outside, to ensure the normal operation of internal pressure and temperature, and to stabilize the oxygen content in the discharge.
The temperature control system is more and more used in the drying of bricks. The thermocouple is connected to the computer temperature display, and the temperature data of each drying section can be known at any time. Based on this, timely adjustment is brought to the standard and efficient drying operation. convenient.
The thermocouple is installed on the top and lower side of the drying kiln, and the specific positions are: near the heating fan, the exhaust flue, 3 parking spaces, 8 parking spaces, 15 parking spaces, 21 parking spaces, and 26 parking spaces.
Several observation windows are set on the top of the drying kiln and on the wall of the kiln to keep abreast of the internal temperature and humidity conditions, so as to be targeted for proper operation.
The position of the observation window is: 3, 5, 7, 9, 11, 12, 15 parking spaces, and the corresponding position of the observation port is preferably the blank stack fire channel, which provides convenience for expanding the observation area.
Environmental emission requirements are becoming stricter and stricter, and the brick and tile industry is no exception. The drying kiln should be considered at the beginning of the construction and design, such as the desulfurization and dust removal devices are large in size and heavy, and it is more appropriate to install under the drying kiln.
The regulation of oxygen content starts from blocking the air leakage point and guiding the digestion. The kiln wall, kiln roof, kiln door and moisture exhaust flue should be airtight and tight, and the observation ports that are not used temporarily should be pasted. In some drying kilns, a moisture exhaust fan is installed between 2-6 parking spaces at the billet inlet end, and the exhausted flue gas is transported to the kiln end of the roasting kiln to be used as combustion air for secondary combustion, which has a significant oxygen reduction effect.
The tidal exhaust fan only extracts the gas from a few parking spaces close to the kiln door, intercepting the excessive oxygen caused by the leakage of the kiln door, and only extracts the gas at the initial stage of drying, which contains relatively small flue gas and moisture, and is transported to The roasting kiln has little effect on roasting as combustion air. After the 6th parking lot, another damp exhaust fan is responsible for the exhaust, and the extracted flue gas is transported to the outside for desulfurization and dust removal.
Newest
- 2023-07-31
Properties of silicon nitride and its application in refract···...
- 2023-07-31
Properties of silicon nitride and its application in refract···...
- 2023-07-31
Properties of silicon nitride and its application in refract···...
- 2023-07-31
Properties of silicon nitride and its application in refract···...
- 2023-07-31
To explore the application of magnesia carbon brick in refra···...
Solution
- 2022-11-22
The technical requirements and production processes of fused···...
- 2022-09-06
Price Determinants of high alumina fire bricks...
- 2022-08-30
Technical performance and technology of silica mullite brick···...
- 2022-08-27
Refractory materials in various parts of the furnace and pre···...
- 2022-08-23
Magnesite chrome brick composition process classification...