How to choose refractory materials for cement kiln
Industry news | Refractory Wiki | Refractory news | Enterprise news | How to choose refractory materials for various parts of cement kiln
1. Pre-tropical zone and decomposition zone
The temperature of these two places is relatively low, and the brick lining is required to have low thermal conductivity and good wear resistance. In this area, the alkali sulfate and alkali chloride from raw materials and fuels begin to volatilize, condense and concentrate in the kiln, and penetrate into the bricks. internal. Ordinary clay bricks react with alkali to form potash nephrite and leucite, which make the brick surface crisp, and the brick body swells and causes cracking and peeling. When alkali-resistant bricks or alkali-resistant insulation bricks containing Al2O325%-28% and SiO265%-70% react with alkali at a certain temperature, a high-viscosity glaze layer is immediately formed on the surface of the brick to prevent peeling. But this kind of brick cannot withstand the service temperature above 1200 degrees Celsius. Therefore, the preheating zone generally uses phosphate-bonded high alumina bricks, anti-stripping high alumina bricks or alkali-resistant bricks.
The decomposition zone generally uses high alumina bricks with good peeling resistance. Silica-mold bricks are better than high alumina bricks with good peeling resistance in terms of performance. The tail feed inlet should adopt anti-skinning silicon carbide castable.
2. Transition zone and firing zone
The transition zone kiln skin is unstable, and the kiln lining is required to have good resistance to atmosphere changes, good thermal shock resistance, low thermal conductivity and wear resistance. It is recommended to use magnesia-aluminum spinel bricks abroad, but the bricks have high thermal conductivity, high temperature of the cylinder, and relatively large heat consumption, which is not conducive to reducing energy consumption. The domestic silicon-mold brick has low thermal conductivity and wear resistance, and its performance is comparable to imported materials to a certain extent.
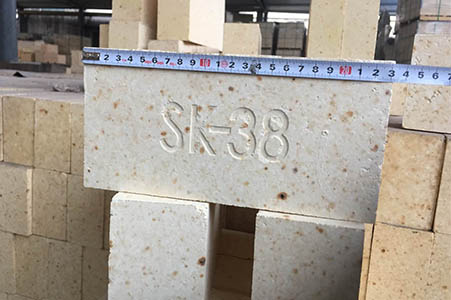
The temperature of the burning zone is high and the chemical reaction is fierce. The brick lining is required to have strong resistance to clinker erosion, SO3 and CO2. Magnesia-aluminum spinel bricks are generally used in foreign countries, but it is difficult for the bricks to hang kiln skins, while dolomite bricks have poor thermal shock resistance and are easy to hydrate; foreign magnesia-iron spinel bricks have better effects on kiln skins. , But the cost is too high. The low-chromium periclase composite spinel bricks newly adopted in China are in better use.
3. Cooling zone and kiln mouth
The temperature at the cooling zone and the kiln mouth is as high as about 1400 degrees Celsius, the temperature fluctuates greatly, and the grinding of clinker and the erosion of air flow are very serious. The brick lining is required to have low thermal conductivity, good wear resistance and thermal shock resistance; alkaline bricks with excellent thermal shock resistance, such as spinel bricks or high alumina bricks, are suitable for use in the cooling zone. Spinel bricks are generally recommended abroad, but spinel bricks have high thermal conductivity and poor wear resistance. In recent years, most of the domestic use of silicon abrasive bricks and wear-resistant bricks with good peeling resistance.
The kiln mouth is mostly castable with good thermal shock resistance. Such as wear-resistant and thermal shock resistant high alumina bricks or steel fiber toughened castables and low cement high alumina castables, but in large kilns with extremely high kiln mouth temperatures, ordinary or steel fiber toughened corundum is used Castable.
1. Pre-tropical zone and decomposition zone
The temperature of these two places is relatively low, and the brick lining is required to have low thermal conductivity and good wear resistance. In this area, the alkali sulfate and alkali chloride from raw materials and fuels begin to volatilize, condense and concentrate in the kiln, and penetrate into the bricks. internal. Ordinary clay bricks react with alkali to form potash nephrite and leucite, which make the brick surface crisp, and the brick body swells and causes cracking and peeling. When alkali-resistant bricks or alkali-resistant insulation bricks containing Al2O325%-28% and SiO265%-70% react with alkali at a certain temperature, a high-viscosity glaze layer is immediately formed on the surface of the brick to prevent peeling. But this kind of brick cannot withstand the service temperature above 1200 degrees Celsius. Therefore, the preheating zone generally uses phosphate-bonded high alumina bricks, anti-stripping high alumina bricks or alkali-resistant bricks.
The decomposition zone generally uses high alumina bricks with good peeling resistance. Silica-mold bricks are better than high alumina bricks with good peeling resistance in terms of performance. The tail feed inlet should adopt anti-skinning silicon carbide castable.
2. Transition zone and firing zone
The transition zone kiln skin is unstable, and the kiln lining is required to have good resistance to atmosphere changes, good thermal shock resistance, low thermal conductivity and wear resistance. It is recommended to use magnesia-aluminum spinel bricks abroad, but the bricks have high thermal conductivity, high temperature of the cylinder, and relatively large heat consumption, which is not conducive to reducing energy consumption. The domestic silicon-mold brick has low thermal conductivity and wear resistance, and its performance is comparable to imported materials to a certain extent.
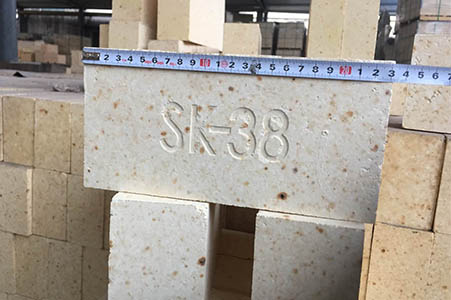
3. Cooling zone and kiln mouth
The temperature at the cooling zone and the kiln mouth is as high as about 1400 degrees Celsius, the temperature fluctuates greatly, and the grinding of clinker and the erosion of air flow are very serious. The brick lining is required to have low thermal conductivity, good wear resistance and thermal shock resistance; alkaline bricks with excellent thermal shock resistance, such as spinel bricks or high alumina bricks, are suitable for use in the cooling zone. Spinel bricks are generally recommended abroad, but spinel bricks have high thermal conductivity and poor wear resistance. In recent years, most of the domestic use of silicon abrasive bricks and wear-resistant bricks with good peeling resistance.
The kiln mouth is mostly castable with good thermal shock resistance. Such as wear-resistant and thermal shock resistant high alumina bricks or steel fiber toughened castables and low cement high alumina castables, but in large kilns with extremely high kiln mouth temperatures, ordinary or steel fiber toughened corundum is used Castable.
Newest
- 2023-07-31
Properties of silicon nitride and its application in refract···...
- 2023-07-31
Properties of silicon nitride and its application in refract···...
- 2023-07-31
Properties of silicon nitride and its application in refract···...
- 2023-07-31
Properties of silicon nitride and its application in refract···...
- 2023-07-31
To explore the application of magnesia carbon brick in refra···...
Solution
- 2022-11-22
The technical requirements and production processes of fused···...
- 2022-09-06
Price Determinants of high alumina fire bricks...
- 2022-08-30
Technical performance and technology of silica mullite brick···...
- 2022-08-27
Refractory materials in various parts of the furnace and pre···...
- 2022-08-23
Magnesite chrome brick composition process classification...